Application cases of industrial endoscopes
- Share
- publisher
- JEET Videoscope
- Issue Time
- Feb 23,2021
Summary
Industrial endoscopes have a wide range of uses. They can be used to inspect the inner surface of industrial products, the inner surface of welds, the inner surface of pipes, the inside of equipment, as well as to inspect redundant objects, check operating conditions and quality control assembly.
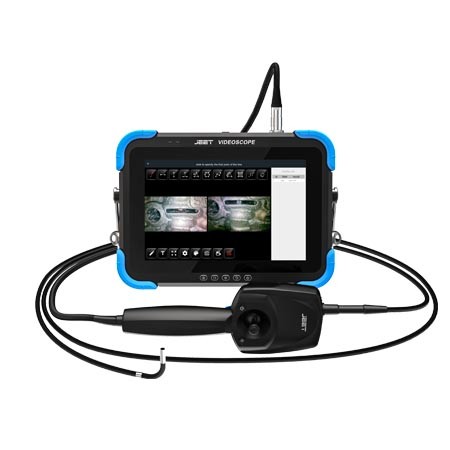
Industrial endoscopes have a wide range of uses. They can be used to inspect the inner surface of industrial products, the inner surface of welds, the inner surface of pipes, the inside of equipment, as well as to inspect redundant objects, check operating conditions and quality control assembly. Then, the following example illustrates its common specific applications:
1. Internal cavity inspection:
Various mechanical parts and raw materials usually produce various damages or defects during manufacturing, storage, assembly and use. The endoscope is used for inspection and can directly see the internal surface conditions, such as cracks, peeling, pull lines, scratches, pits, bumps, spots, corrosion, etc. It is usually used in inspection methods with other non-destructive testing, and the test results are more accurate . For example, in the auto parts industry, industrial endoscopes are widely used.
2. Assembly inspection:
After the parts are assembled, check whether the internal parts meet the drawing requirements and whether there are assembly defects. Power equipment has many applications. At the same time, endoscopy can also be used during equipment maintenance, such as power cabinet inspection, GIS electrical equipment inspection, transformer short-circuit failure, etc.
3. Welding inspection:
At the welded joints of the pipe connection, problems such as cracks, incomplete penetration, raised welds, weld leakage, weld slag, wrong edges, pores, splashes, etc. may occur. You can use the endoscope to directly observe the surface condition. It can also be used to observe internal surface defects, such as oxidation color, internal blockage, etc.
4. Redundancy check:
Check all kinds of metal, non-metal residues, residual internal debris, foreign objects in the component cavity. Such as screws, tools, sundries, etc. falling into the equipment, burrs during processing, liquid residues in the pipe after cleaning, etc., these foreign objects can be removed by hooks or pliers (customized) at the front end. Endoscope.
5. Processing inspection:
Various surface defects produced in the process of processing various mechanical parts, such as fine burrs of the intersecting holes of the runners, surface damage, flanging, etc.
6. Status check:
Detect the operating status of the equipment in use, as well as the surface conditions and internal defects of various buildings. In many cases, the endoscope can even observe the inside of the device without stopping the operation of the device, thereby avoiding losses caused by shutdown.
Since its establishment, Jeet has always insisted on independent innovation, and formed a continuous innovation mechanism through effective use of the independent intellectual property rights of its leading products to maintain its leading position in the industry. The products have been widely used in various fields and have won a good reputation. In the future, we will continue to pay attention to customer needs and provide users with better products and considerate services.